Experience of Produce Architecture Laminated Glass with PVB Film
Xinbohong, a laminated glass manufacturer with over 20 years of experience in the industry, is one of our esteemed clients. Their Chief Engineer Mr.Leo recently shared with us the wealth of knowledge and insights they have accumulated in the production of laminated glass. Here’s a glimpse into the expertise and meticulous processes that have made them leaders in their field.
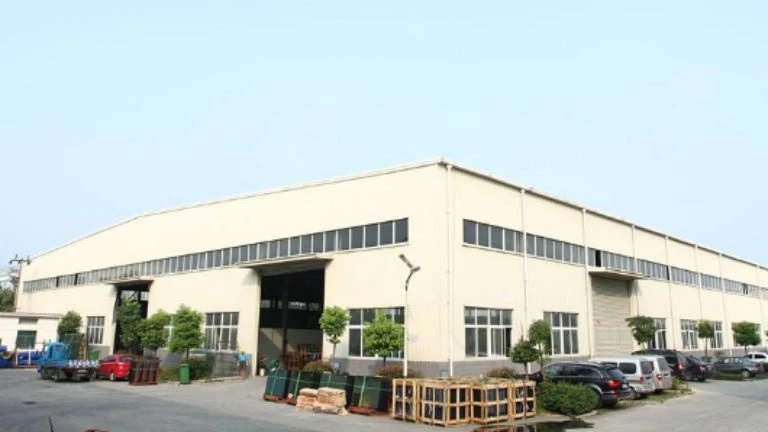
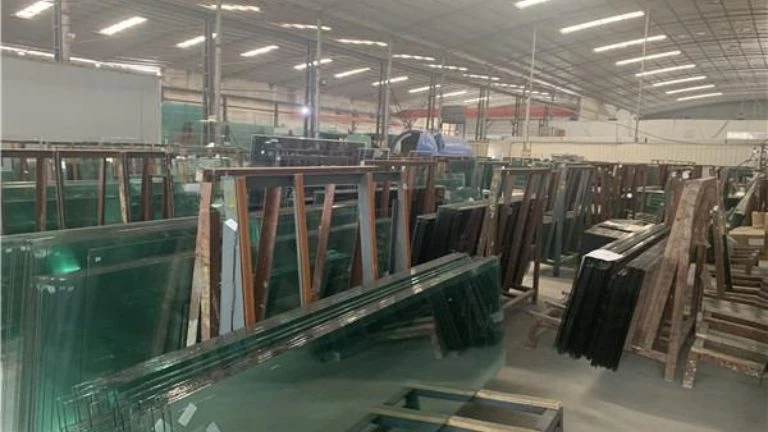
Mastering the Art of Laminated Glass: Insights from a Veteran Manufacturer
Mr. Leo: In the world of architectural glass production, maintaining the pristine condition of the lamination room is paramount. Our experience has taught us the importance of shielding PVB (Polyvinyl Butyral) films from direct sunlight and keeping the room’s temperature finely tuned between 20°C to 26°C. Equally crucial is managing the relative humidity to stay within the 25% to 40% range. These conditions are vital for ensuring the PVB film’s moisture content hovers between 0.4% to 0.6%, which is essential for optimal lamination results.
When it comes to the actual lamination process, precision and care are our guiding principles. The process begins with laying the glass flat and carefully spreading the PVB film over it. Another glass piece is then placed on top, and any excess film is meticulously trimmed with a small knife. Through experience, we’ve learned the importance of handling the film gently during trimming to prevent deformation and the formation of air bubbles. Ensuring a 2-3mm excess of film around the glass edges is a small but critical detail that makes a significant difference. A key tip we’ve discovered is to avoid direct contact between the trimming knife and the glass, as this can lead to micro particles that cause bubbles along the processed edges.
Top Press Deaeration is a step that cannot be overlooked. The assembled glass must be subjected to this process to expel any residual air trapped between the glass and film interface, ensuring a seamless edge seal before high-pressure forming. Our preferred method is roll press deaeration, which involves preheating the glass assembly before it passes through a series of rollers that squeeze out any remaining air, ensuring a perfect seal. A clear band around the perimeter of the laminated glass post-deaeration is a telltale sign of a job well done, preventing any potential gas backflow from creating bubbles in the autoclave.
The Double Set Rubber Roller Process is where the magic of temperature and pressure finely intertwines. The film’s behavior at different temperatures—turning semi-transparent between 60°C to 90°C and transparent above 90°C—has taught us the delicate balance required. The temperature must be just right to avoid premature edge sealing or, conversely, incomplete sealing that leads to backflow bubbles. We’ve fine-tuned the gaps in the rubber rollers and the temperature and pressure settings to ensure the laminated glass emerges flawless. Running the glass at a speed of 400-700 rotations per hour has proven optimal.
Our production strategy is to prepare the required glass in advance and maintain a continuous, uninterrupted workflow. This approach helps prevent the drastic temperature fluctuations in the constant temperature box that can complicate the control over the glass surface temperature. These insights are the culmination of years of dedication and refinement in the art of glass lamination, ensuring that each piece we produce meets the highest standards of quality and safety.