Producing Bent | Curved Laminated Glass with PVB Film
The production of bent laminated glass using PVB film is a complex but rewarding process that requires precision, expertise, and advanced technology. From the careful bending of glass to achieve the perfect curvature to the meticulous lamination process that bonds the glass with PVB film, each step is crucial in creating a product that combines beauty with functionality. The result is a durable, safe, and visually appealing glass suitable for a wide range of applications, from stunning architectural designs to safety-critical automotive windows.
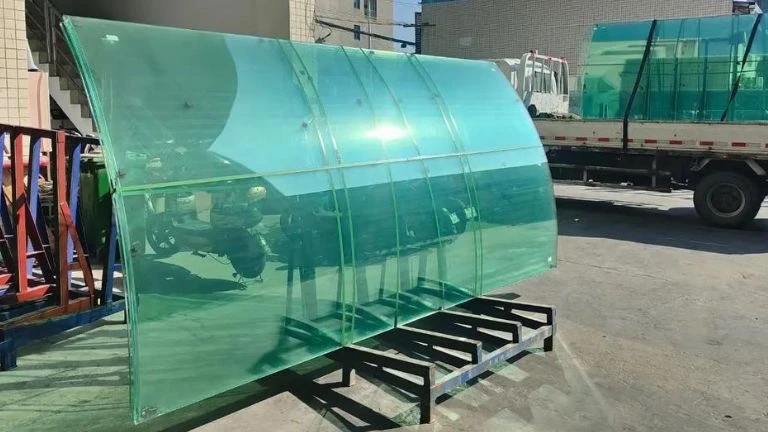
The Bending Process
The journey to producing bent laminated glass begins with the meticulous bending of glass sheets. This process requires precision and careful control to achieve the desired curvature without compromising the glass’s integrity. The glass sheets are first cut to size and then undergo an extensive cleaning process to remove any impurities that could affect the final product’s quality.
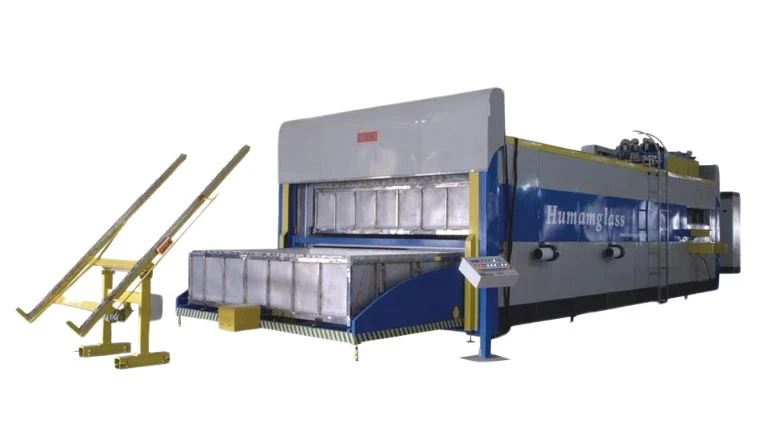
Once prepared, the glass sheets are placed in a bending kiln, where they are heated to a specific temperature that makes them pliable, typically between 500°C to 600°C (932°F to 1112°F). Achieving uniform heat distribution is crucial at this stage; any inconsistencies can lead to thermal stress, causing the glass to warp or even break. To prevent this, manufacturers use sophisticated, computer-controlled kilns that ensure even heating and monitor the glass’s temperature throughout the process.
When the glass reaches the desired malleability, it is carefully shaped over or into molds that match the required curvature. This step must be executed with precision, as the glass’s final shape is determined here. Once shaped, the glass is slowly cooled in a controlled environment—a process known as annealing—to relieve any internal stresses and solidify its new form. This gradual cooling is essential for maintaining the glass’s structural integrity and ensuring its durability.
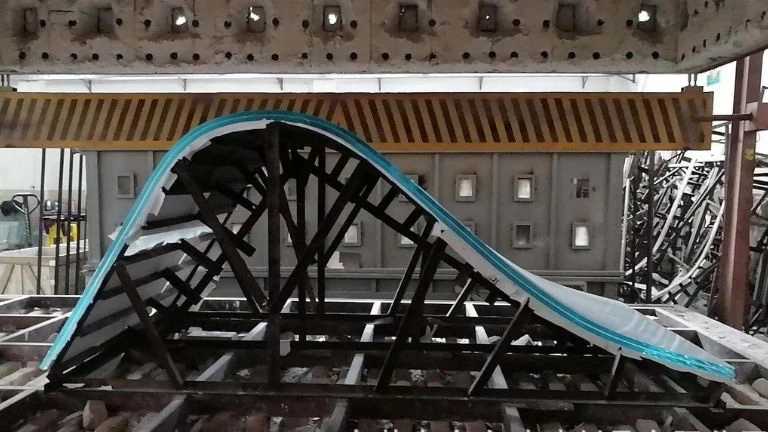
The Lamination Process
Following the successful bending of the glass, the next step is lamination, where the bent glass sheets are bonded with PVB film to create a strong, cohesive unit. PVB is chosen for its excellent adhesive properties, clarity, and its ability to hold shattered glass fragments together upon impact, significantly enhancing the safety of the final product.
The lamination process starts with the meticulous assembly of the glass “sandwich.” A layer of PVB film is placed between two bent glass sheets, ensuring no air bubbles or wrinkles are present, as these can affect the glass’s appearance and structural integrity. Achieving a perfect alignment is particularly challenging with curved surfaces, requiring skilled technicians and the right tools.
To assist in this process, the assembled glass “sandwich” often undergoes a pre-lamination phase which includes pre-heating and pre-pressing in a vacuum bag or box. This step is crucial for eliminating air pockets and ensuring a tighter bond between the glass and PVB layers before the final lamination.
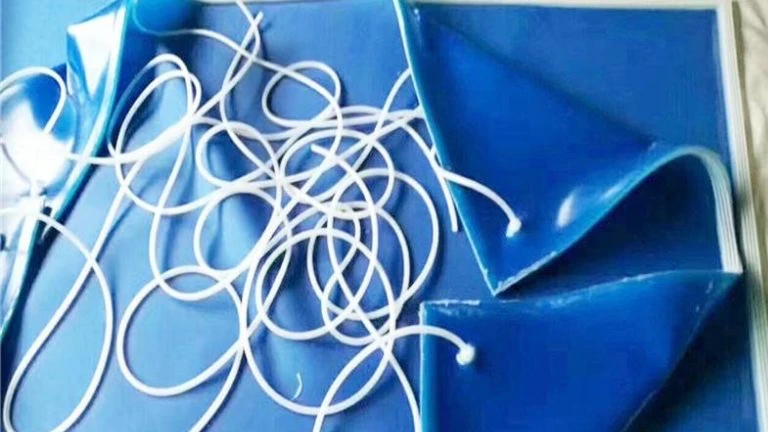
The assembled “sandwich,” now pre-heated and pre-pressed to remove as much air as possible, is then placed in an autoclave, a specialized chamber that applies heat and pressure to bond the glass and PVB layers together. The conditions within the autoclave—temperature, pressure, and duration—are carefully controlled to ensure the PVB film adheres perfectly to the glass, creating a uniform bond across the entire surface. This step not only enhances the glass’s strength but also ensures it remains intact in the event of breakage, with the PVB film holding the broken pieces together.