How to open a laminated glass factory
Equipment, Infrastructure, and Factory Size Requirements for Laminated Glass Factories
Overview
Laminated glass, widely used for safety purposes in both architectural and automotive applications, has witnessed a growing demand with the improvement in living standards. This article aims to provide aspiring laminated glass factory owners with concise insights into the necessary equipment, facility size, and workforce requirements.
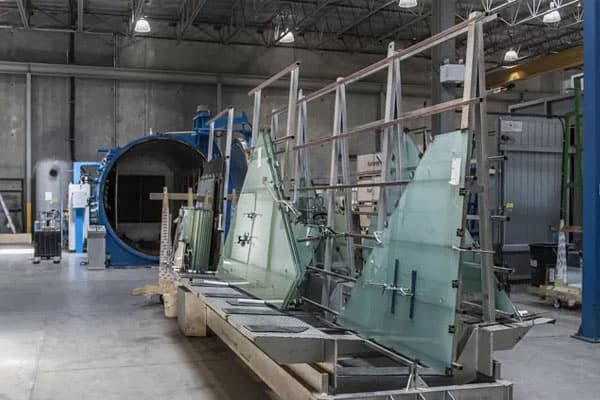
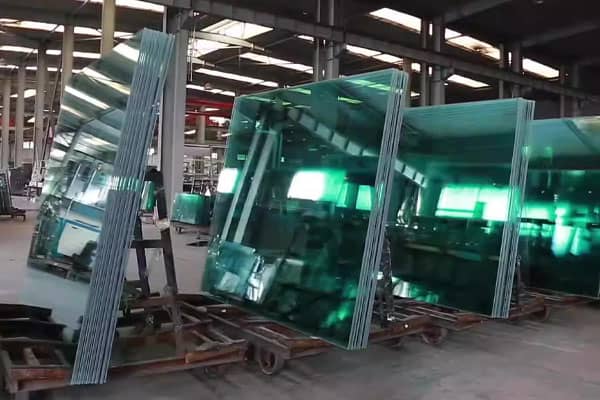
Equipment Requirements:
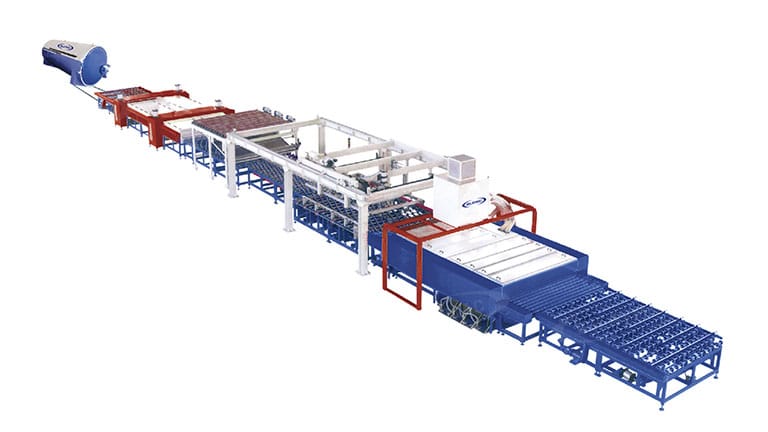
Glass Cutting Machine:
A glass cutting machine is essential for cutting the raw glass into the desired sizes and shapes.
Edging Machine:
An edging machine is used for smoothing and shaping the edges of the laminated glass for a finished appearance and safety.
Washing Machine:
This equipment is used to clean the glass after cutting to ensure a clean surface for lamination.
Tempering Furnace:
(If produce tempered laminated glass)
A tempering furnace is essential to increase the glass’s strength and safety properties.
Glass Heat Bending Equipment
(if producing heat-bent laminated glass)
Used for heating and shaping glass in heat-bending applications.
Laminating Production Line:
The core of laminated glass manufacturing, this production line consists of several key components:
- Adhesive Application Machine: Responsible for evenly spreading adhesive, usually a Polyvinyl Butyral (PVB) interlayer, on the glass surfaces.
- Glass Laminating Machine: It brings together multiple glass layers with the interlayer material and removes air bubbles, ensuring proper adhesion.
- Autoclave or Oven: This equipment is utilized for curing and consolidating the laminated glass under heat and pressure.
Quality Control and Testing Equipment:
Quality control is paramount, and it involves various testing equipment, including:
- Optical Inspection Systems: Used to assess surface quality, detect defects, and ensure a flawless appearance.
- Impact Testing Machines: For evaluating the impact resistance and safety properties of the laminated glass.
- UV Testing Equipment: Assessing resistance to UV radiation, especially important for outdoor applications.
- Thickness Measurement Tools: Ensuring product specifications adhere to precise requirements.
- Interlayer Bond Strength Testers: To verify the adhesive strength between glass layers and interlayer material.
Packaging Equipment:
Necessary for safely packaging and storing the finished laminated glass products, ensuring they reach customers in optimal condition.
Infrastructure Requirements:
Factory Space: The factory’s size is contingent upon the production scale and product diversity. Smaller laminated glass facilities may require 2,000 to 5,000 square meters, while larger operations might span 10,000 square meters or more.
Electricity Supply: The energy-intensive nature of laminated glass manufacturing demands a reliable and stable electrical supply to power the equipment.
Water Supply: A reliable water source is essential, as it’s used in the glass washing and cleaning processes.
Emission Control Facilities: To meet environmental regulations, systems must be in place for wastewater treatment and emissions control.
Safety Facilities: Equip the factory with safety equipment, emergency response tools, and fire safety measures to maintain a secure working environment.
Workforce Requirements:
The number of employees required for a laminated glass factory depends on the scale of production, the complexity of manufacturing processes, and the level of automation. Here are some general guidelines:
Small-Scale Factory: A small-scale laminated glass factory typically employing fewer than 20 people may have a more simplified production process, relying on basic equipment and limited product variations. A small team can handle tasks such as glass cutting, laminating, quality control, and packaging.
Medium-Scale Factory: A medium-scale factory with an employee count ranging from 20 to 50 may have a more diverse product range and more advanced equipment. In addition to the roles in a small-scale factory, it may require specialized positions such as machine operators, maintenance technicians, and quality control specialists.
Large-Scale Factory: A large-scale laminated glass factory, employing over 50 people, operates with a high degree of automation and complexity. In addition to roles mentioned earlier, it might include engineers, logistics personnel, administrative staff, and a larger quality control team to maintain the efficiency of the production process and ensure product quality.
In addition to the general workforce requirements, it’s crucial to highlight the need for at least one experienced professional in the processes of tempering and lamination.